-
13603466949 在線咨詢
氮化錳片
氮化錳指標 氮含量5-7% 錳含量70-90% 可根據客戶要求定制...
-
13603466949 在線咨詢
氮化錳球
氮化錳指標 氮含量5-7% 錳含量70-90% 可根據客戶要求定制...
-
13603466949 在線咨詢
螢石球
冶金級螢石球是為解決冶煉過程中透氣、環保、易操控及低磷低硫等特別要求,由冶金級螢石精粉加無機物粘合制造而成。它替代螢石塊礦被廣泛用于鋼鐵冶煉、有色金屬冶煉、鐵合金冶煉、化鐵工藝生產等行業。品級CaF2...
-
13603466949 在線咨詢
螢石球
冶金級螢石球是為解決冶煉過程中透氣、環保、易操控及低磷低硫等特別要求,由冶金級螢石精粉加無機物粘合制造而成。它替代螢石塊礦被廣泛用于鋼鐵冶煉、有色金屬冶煉、鐵合金冶煉、化鐵工藝生產等行業。品級CaF2...
-
13603466949 在線咨詢
純鈣包芯線
發展歷史 純鈣線(金屬鈣實芯包芯線) 實芯純鈣芯線,上世紀70年代被國外鋼廠用于鋼水的處理,到今已在世界上廣泛應用,特別是在上世紀90年代薄板連鑄技術的興起和快速發展,實芯純鈣芯線的優勢已被多數有...
-
13603466949 在線咨詢
硅鈣包芯線
1.產品介紹由硅鈣合金加工成粉由帶鋼包裹后,經包芯線機加工而成;2.優 勢①.適用于煉鋼脫氧、脫硫,可改變鋼的性能,提高鋼的塑性、沖擊韌性和鋼水的流動性,還能直接進入鋼液內熔化、分布均勻;②.保留了硅...
主營合金包芯線、純鈣包芯線、硅鈣包芯線、硅鐵、脫氧合金、煉鋼輔料產品
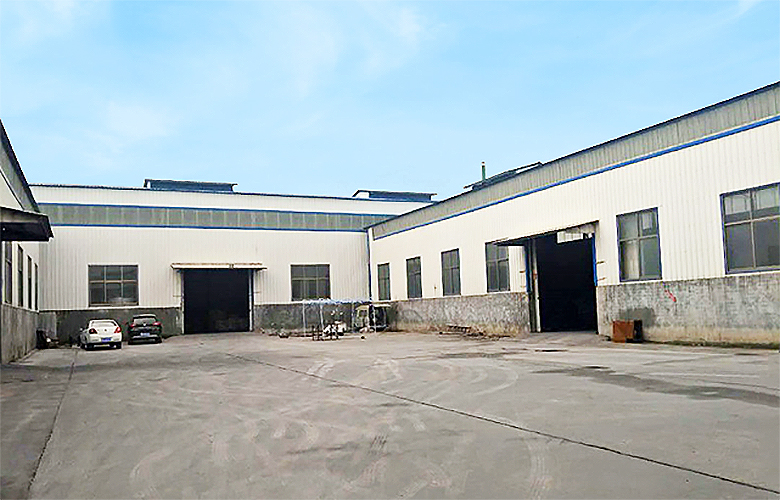
安陽市宏遠實業有限公司位于甲骨文發源地——古都安陽,地處晉冀魯豫四省交界,京廣鐵路,107國道貫穿境內,交通便利,通信發達。公司現有固定資產1500萬元,職工100人,其中工程師8人,技術人員11人,本公司遵循“誠信為本、質量保證”的經營方針,深受廣大用戶好評。 我公司是一家主要從事合金包芯線、純鈣包芯線、硅鈣包芯線、硅鐵、脫氧合金、氮化合金、煉鋼輔料的研發及加工廠家,公司現擁有成熟的氮化物......
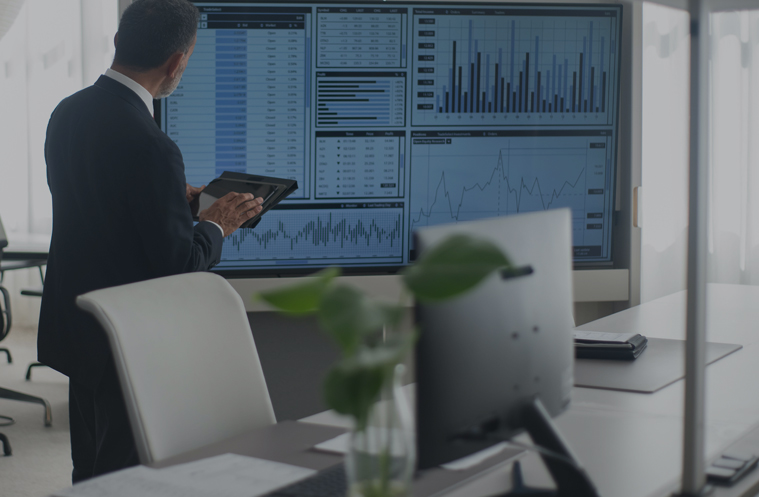